MELBOURNE, Fla. – Frank works hard building houses, often for long hours at a time, without complaining. He completes his work in a fraction of the time it takes traditional homebuilders. What gives him his edge?
Frank is a robot, and he’s building his houses using 3D printing technology.
Trevor Ragno is Frank’s boss. Ragno is the head of construction and building technology for Apis Cor, based in Melbourne, Florida.
Apis Cor is one of several companies that offer the cutting-edge construction technology.
“There’s a lot going on in here,” Ragno said as he walked into a home that was just printed by Frank. “Right now, we’ve just kind of walked into a living room. We could take a couple more steps forward and we have a viewing area for kind of a living room. We have a TV that’s being mounted here, a recessed fireplace. We have actually 3D printed some components on the ground, which are our mantel going across here, and an arch in the back that will go up top.”
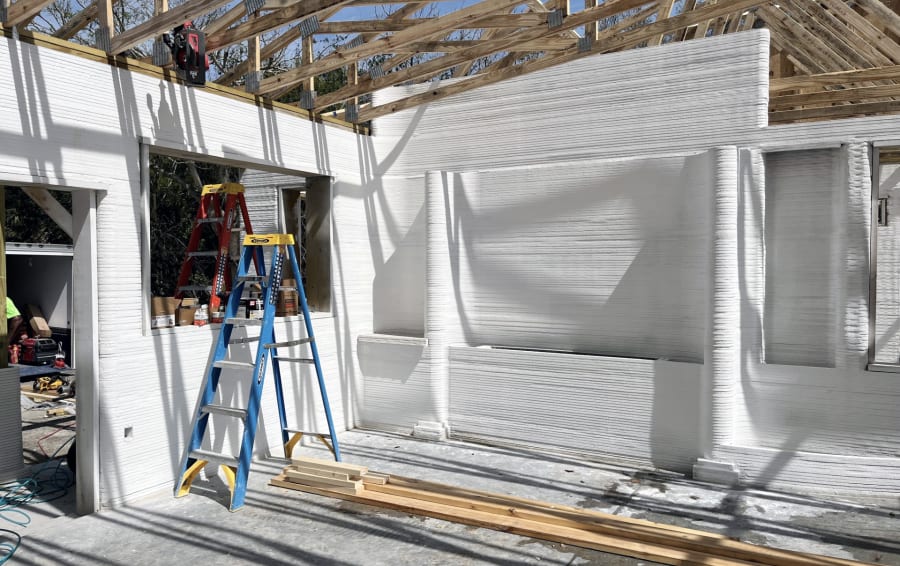
Frank layers rows and rows of concrete, which stack to form the walls of the house, both inside and outside. His technology helps bring down the rising costs of real estate.
“We’re about 30% more affordable than what our neighbors are per square foot,” Ragno said.
He pointed to a home nearby that was about to go on the real-estate market.
The three-bedroom, two-bath home with 1,500 square feet was built in the 1980s, and it will be advertised at $440,000.
The brand new home Frank built is a four-bedroom, four-bathroom house with 2,100 square feet of space. Ragno said it will be offered for sale at $305,000 — a savings of $135,000. He said 3D printing the home allows the builder and the prospective homeowner more flexibility in design — and shorter construction times.
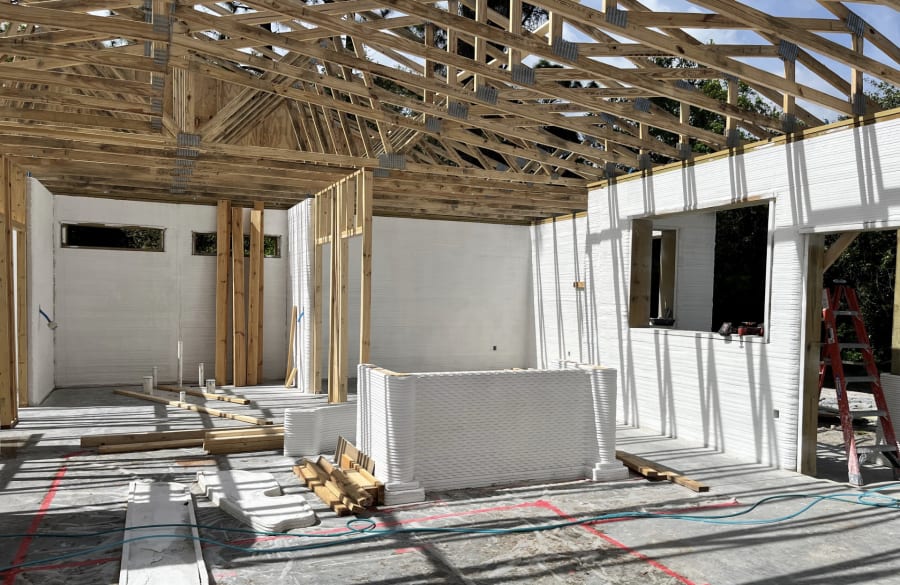
Ragno said the structure is strong enough to endure hurricane-force winds and earthquakes.
Most of the 3D printed buildings in the world have been constructed in North America, but building codes have not kept up with the technology, making it challenging in some areas of the U.S. The need for fewer construction workers also means fewer jobs where the homes are built.
Ragno said there is another limitation.
“I’d say our biggest challenge is making enough robots to satisfy demand for people,” he said. “When you’re starting to build technology of this scale — it’s not necessarily a cellphone case you’re making or something like that — it’s a very serious piece of technology that we want people to be able to use for a long time.
“It’s tough to say a solution like any one thing can solve all problems,” he said. “It does make a difference, and that’s all that we can try to do. Just make the best technology we can and get people homes.”
This article is part of “Solutionaries,” our continuing commitment to solutions journalism, highlighting the creative people in communities working to make the world a better place, one solution at a time. Find out what you can do to help at SolutionariesNetwork.com.